Knowledge gained from frequent utilization of FRP for mold fabrication, years of in-house expertise for large constructions with unusual applications, plus our “project” orientation have lead us to consider and accept a wide range of challenging proposals for FRP and related products.


We successfully contributed to the design and configuration of eighteen (18) foot diameter hemispheric projection screens (for Immersive Graphics) which are currently in operation at a major attraction. Further, we built the tooling, molded a total of nineteen complete sets, transported, assembled/finished, and finally mounted and painted them in place. Our ability to vertically integrate the complete project provided continuity and consistency which saved the customer untold dollars.
At the other end of the spectrum; we have, in significant numbers and on tight production schedules, built Carbon Fiber tubes, contracted for injection molded and non-standard steel attachment components, and then assembled three stage telescoping wands that were integral to a state of the art land mine detector for a major military contractor. Our follow up to that project was to assist with the tooling and CF component parts aspect of a weight reduced sweep wherein the device went from 11lb 8oz down to 5lbs 14oz.
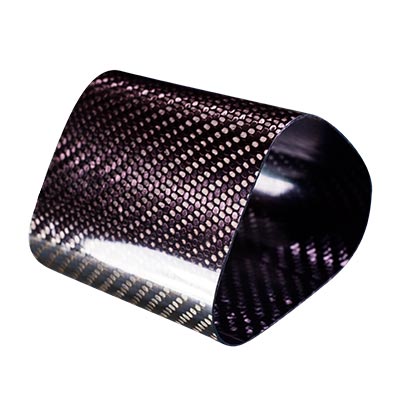


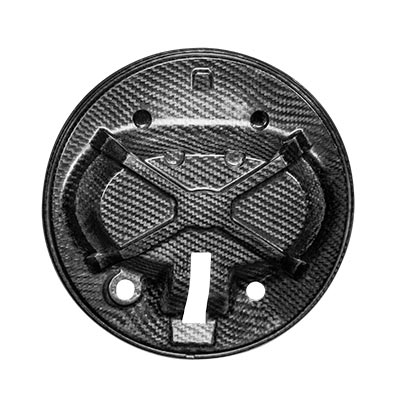
Consequent to our experience, the production of FRP armatures which are often necessary for molded parts are rarely, if ever, a problem for parts we are processing. The ability to source and produce parts and armatures on parallel courses saves time, avoids confusion, and ultimately reduces cost.
Our ability to undertake large, time sensitive missions, and deliver quality products which meet very strict specifications is a point of pride. There are, in fact, very few constraints to the type or size jobs we will consider. Our expertise with multiple materials and processes (inclusive of an in-house capacity for RTM tooling and parts) give us the tools we need to do them.